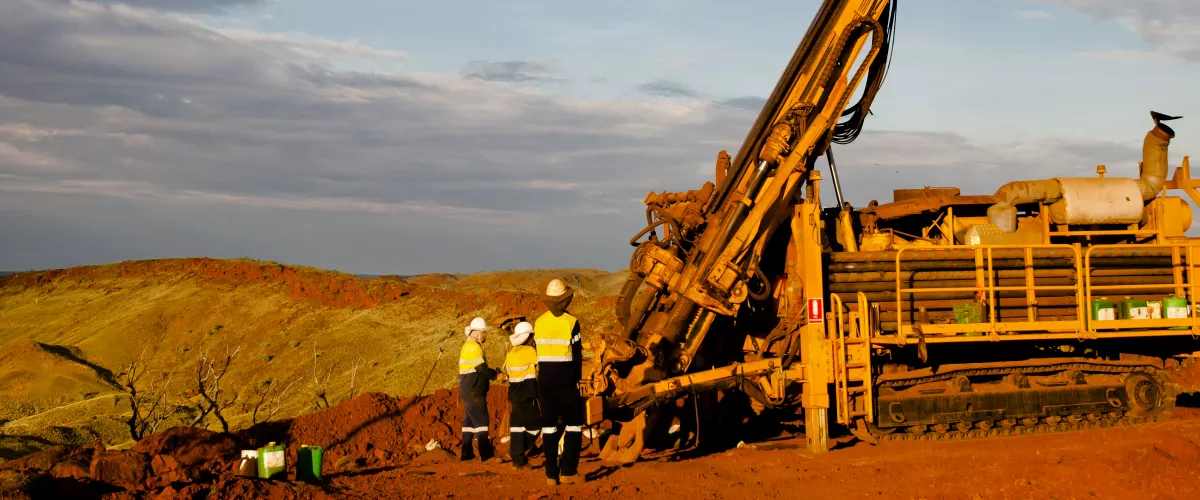
How Toll delivered a truly global cross-border solution to help a multinational mine site avoid losing millions of dollars.
Deep in the Australian outback in a remote part of central Queensland that’s steeped in dry, red earth is a multinational mine site. The site plays a vital role in global high-value mineral and resources production, and it is all kept humming by a series of giant furnaces.
Every five years or so, each of these hard-working furnaces must be entirely relined, brick by brick, using specialised materials that are shipped from the other side of the world. Thousands of individual pieces are delivered in carefully sequenced truckloads to precise areas on site. From here, the bricks of varying shapes and sizes are carefully set in place.
Toll’s Senior VP for Toll Global Forwarding Projects, Paul Crowley, says timing is critical from the moment the bricks are ready for shipping from the factory in Austria, until the second they are delivered on site in central Queensland.
“Because the production times for these kiln bricks are unpredictable, the final date for shipping isn’t usually clear until the timeframe is very tight,” says Paul, who has been working closely with the customer for more than a decade.
Our biggest task for this customer was to get sufficient space onto shipping lines in three different vessels to get them to Australia at a time when there was a chronic space shortage for shipping worldwide, especially out of Europe.
Paul Crowley, Senior VP for Toll Global Forwarding Projects
Our team at Toll applied the full force of our logistics nous, securing one shipping lane from Antwerp, Belgium, another from Hamburg, Germany, and a third from Trieste in Italy – along with the associated road freight criss-crossing Europe to arrive at these ports – to load a total shipment of 821 pallets of bricks packed in 91 TEU (Twenty-foot Equivalent Units of 44 x 40’ containers and 3 x 20’ containers).
When these ships arrived into ports in Sydney and Brisbane, the first critical step was to have the cargo fumigated against the brown marmorated stink bug, which are considered a risk for all freight originating from Europe at certain times of year.
“Because of the tight shipping times, we had to perform the quarantine arrangements in Sydney and Brisbane,” Paul says.
Our next challenge was sourcing warehouses large enough to unpack the bricks under cover.
“The bricks are not allowed to get wet, so we needed to unpack the containers under cover in warehouses near the wharfs,” Paul says.
Then the real puzzle began, as bricks of many different shapes and sizes needed to be sequenced and strategically loaded into a combination of semi-trailers, B-Doubles and triple road trains from the two Australian ports to the mine in central Queensland.
The sequencing we did in Sydney and Brisbane is crucial to the whole execution. When the furnace is rebricked, the mine is unable to conduct smelting activities, so minimising this down time is a high priority for the customer. And getting the right bricks at the ready in the right place is key.
Paul Crowley, Senior VP for Toll Global Forwarding Projects
“These bricks fit together like Tetris,”
“Each truck was strategically loaded and set for delivery at a precise area within the mine site. We had detailed instructions, ‘truck 1 has to arrive at the north-east corner’, and ‘truck 8, 9, 10 need to be at these exact points near the kiln’.” Paul says.
“These bricks fit together like Tetris,”
“Each truck was strategically loaded and set for delivery at a precise area within the mine site. We had detailed instructions, ‘truck 1 has to arrive at the north-east corner’, and ‘truck 8, 9, 10 need to be at these exact points near the kiln’.” Paul says.
Toll’s work from Europe to the remote Australian outback concluded as we made deliveries to precise locations across the mine, leaving the well-travelled cargo ready for its next stage. Several hundred bricklayers were at the ready to follow the step-by-step sequencing and rebrick the inside of the circular furnace as quickly as possible. Setting the final pieces in place for this trans-continental puzzle.
Key Insights
of delivering a truly global cross-border solution.
The Challenge
Kilns in an international mining company’s mine and metals smelter at Mount Isa, North Queensland, Australia, need to be relined every five years with bricks from Austria.
The Project
The project required engineers and bricklayers for a 21-day shutdown to address space shortages and international shipping delays, avoiding tens of millions in daily penalties and lost production.
The Solution
The team navigated international shipping hurdles, loading and tracking 47 containers of bricks from Europe to Australia, ensuring customs clearance, fumigation, and delivery within tight schedule.
The Result
The project was completed successfully without incurring extra downtime costs to the customer.